Just north of Seattle, Whidbey Island is one of those places where ocean life and human life merge a little bit more than in most places. Here, in his coastal home studio, designer Craig Woehrle collects observations from the beach below—sea-beaten driftwood lined with softened whorls, clusters of seaweed and mollusks, wave-worn patterns in the rocks and sand. His notebook is filled with sketches of shapes from the Salish Sea, but instead of lifelike doodles Craig draws in parameters within mathematical systems that translate the sea into patterns—a skill he learned at Harvard and parlayed into an unusual career.
Craig’s interest in patterns began while he was working toward his master’s in landscape architecture. While his cohort studied botany, Craig spent most of his time digitizing surface flows (think water and sediment runoff) and manipulating their parameters to study the results. An early studio course introduced him to the technique of making these studies real through digital fabrication—using software to carve the flows into materials that could then be used as decorative architectural features. He was hooked.
Post-grad on Whidbey Island, Craig turned his infatuation into Patternine, a company that aims to push the commercial limits of his design methodology. After seven years on the water he’s become keenly aware of the movements of tides and weather by walking the beach, mentally calculating, and drawing on paper to figure out the parametric structure of his observations.
- Craig acts as a translator, rewriting the visual language of his observations as adjustable parameters and variables within his digital systems and giving nature’s artistry new physical form.
- “There’s a lot of stuff in these sketchbooks; they’re not all designed, but they are stabs at how I would structure those digital experiments that I intend to perform,” Craig says.
- “I look at [Patternine] as art—monolithic, seamless—that could be expanded, blown up, or shrunk based on the application,” Michael says.
“I start to sketch out the digital outline of how those parameters would interact with each other and what I would expect the output to yield,” he says, speaking a hybrid language of mathematics and design. “Creating with design parameters or curve or surface parameters, any adjustment creates aesthetic diversity within the construction of that logic. Tweaking those parameters yields different, sometimes surprising, results.”
To begin producing his work Craig got a shop and a CNC machine and began carving his intensely calculated patterns into solid surface—a manufactured resin material perfect for flat surfaces like countertops or cabinet fronts. It’s also perfect for Craig’s designs: It’s easily carved with standard machinery and is installed without visible seams.
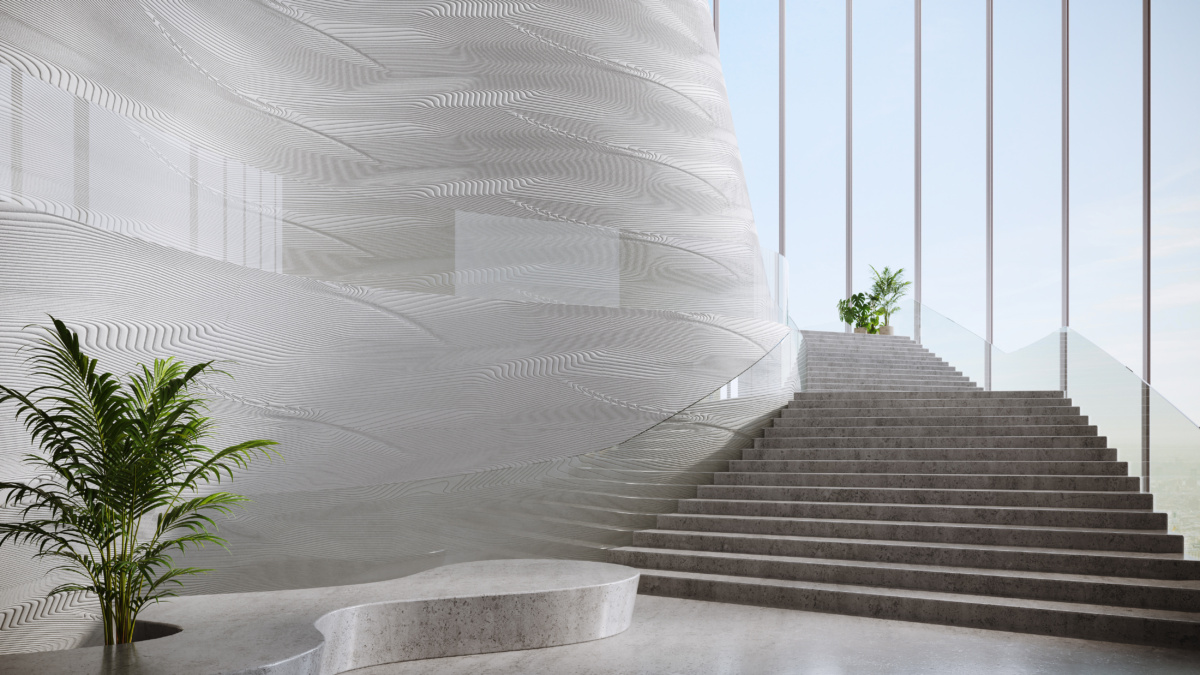
The Patternine patterns can become architectural installations at any scale, making for jaw dropping spaces with a distinct natural influence.
Meanwhile, at solid surface manufacturer Durasein, Michael Bustin and Brandon Guthrie were developing a shop of their own. The creative hub D.Lab presents the possibilities of Durasein’s solid surfaces to inspire architects, designers, and fabricators to get inventive with the material. The aim is to establish a space to show off interesting work and encourage collaboration among their audience to take projects to the next level.
Michael, Durasein’s global chief growth officer, began scouring the internet for work to feature with D.Lab when he spotted Craig’s work on social media mere minutes after he posted it. Michael was mesmerized and immediately saw Patternine as a perfect fit.
The collaboration between D.Lab and Patternine started with a feature on D.Lab’s site and grew into an exclusive partnership. Michael and the Durasein team work closely with Craig to identify opportunities all over the world for Craig’s parametric wall installations made with Durasein’s solid surfaces.
- Craig acts as a translator, rewriting the visual language of his observations as adjustable parameters and variables within his digital systems and giving nature’s artistry new physical form.
- His observations, carved into Durasein solid surface, become easily installed, infinitely scalable surfaces capable of many applications.
While the patterns could go anywhere, they start with Craig’s inspiration from the sand, rocks, storms, and tide patterns on the beaches of Whidbey Island. “My little workspace in this mid-century house that we’re in overlooks the changing water of the Salish Sea. I just look over the monitor and I can see something new because the water’s never the same,” he says.
When building out an experiment Craig considers how the design will translate through the digital fabrication process, thinking through the type of machine it will be cut on (three-axis or five-axis?) and the method of machining (perhaps C-axis aggregate rotation?), which affects the efficiency of fabrication. He considers the shape of the cutting tool, the depth of the cut and resulting shadows, and potential for backlighting. Then he can visualize and test the physical result cut into the 12-millimeter thick Durasein solid surfaces.
- The waters off Whidbey are Craig’s favorite inspiration for surfaces and installations like the one seen at right.
- Even in solid surface form, Patternine products retain an inherently organic feeling.
After some trial and error the patterns find their way into Craig’s catalog, ready to be selected and retooled for site-specific installs. Once Craig is in contact with someone interested in his patterns, he works to tweak the parameters of the chosen design to suit the application—it may need to be scaled up or down, expanded, backlit, or otherwise altered to fit an install site.
Each tweak takes it an inch further from the original pattern, but the lines still contain refracted hints of the oscillating movement of waves or the gentle swirls of ancient driftwood burls. Craig sends the cut files to the fabrication partner nearest to the design’s final destination, and the CNC machines start carving away.
The production system had its first real test with an installation in the offices of a Shanghai architecture firm. The firm has a central hallway, perfect for the eye-catching features Patternine and Durasein offer. With the help of Durasein’s China team and fabrication partners nearby, a backlit design inspired by mussel shells found at Penn Cove on Whidbey was installed seamlessly, despite having a remarkably thin wall to contain the backlighting and affix the installation.
- A refracted Whidbey wave pattern (left panel) and an early design based on flows and sediments Craig observed at Harvard (right panel) illuminate Craig’s foyer.
As the flat surface application of Patternine and Durasein grows in popularity and the production system gets increasingly hammered out, Craig and the Durasein team look forward to what Craig calls phase two—going beyond the standard expectation of wall panels and flat applications to create patterned furniture pieces and products. “Anybody could technically do it as long as you can lay out a parametric design,” Brandon, the marketing director of Durasein USA, says. “But I think the complexity Craig brings to the game from a science perspective, combined with the art of our creative audience, leads things to be quite unlimited in our capabilities as a manufacturer.”
A major capability Durasein products bring to the table is that they can be cast in a mold, like concrete. Imagine a big, freestanding bathtub, but instead of having smooth sides it’s covered in Patternine’s tidal swirls and rippling lines like beach sand. The team envisions patterned landscape elements like planters, seating, and party enclosures as well as hospitality furnishings, shower panels, and, yes, bathtub basins.
- As Patternine and Durasein’s collaboration grows, they hope to expand to new applications of Patternine’s work.
- Eventually, the patterns may even take shape on bathtub basins, planters, and other objects with surfaces that could use a little visual interest.
Craig credits much of the progress and future of Patternine to Durasein’s nimbleness and Michael’s optimism. “He is such an energetic captain, and we’re so simpatico on design and aesthetics.”
The high regard goes strongly in both directions. “We courted Craig because he has this incredible vernacular. When he speaks about the technology side of things it’s like another world, and he understands all of it,” Michael says. “We knew if there was ever an opportunity for us to push our material to do something radical, if we invited him, some of our teammates, and some kickass fabricators, we could sit at the table and dazzle the world’s leading designers and creatives because we understand all of it—the material, construction, design, engineering, parametrics, on and on.”
A version of this article originally appeared in Sixtysix Issue 10 with the headline “Power of Nature.” Subscribe today.