It all started with a stack of wood. Russell Greenberg started design consultancy RUX Studios in 2008, taking on a balance of creative and client work when, a few years later, a light bulb went off. He was immersed in projects—including a design for a house that would ultimately never be built. The house needed a special light fixture, and when Russell saw a pile of wood on the verge of being trashed, he stepped in to repurpose it. From that moment, Stickbulb was born.
Founded in 2012 with Russell and cofounder Christopher Beardsley, one simple and sleek light turned into a beautiful modular system that appealed to the duo’s sensibilities as trained architects. Russell and Chris met in an architecture studio undergraduate program at Yale University, before the young architects set out to design a collection with the least number of parts possible—with connections that make the pieces easy to separate for maintenance, recycling, or reuse. They used reclaimed and sustainably sourced woods and LED technologies, and they manufactured locally in Long Island City. “By limiting the possibilities you’re willing to accept in terms of design solutions, you end up with these very small, beautiful quiet moments that have big effects,” Russell says.
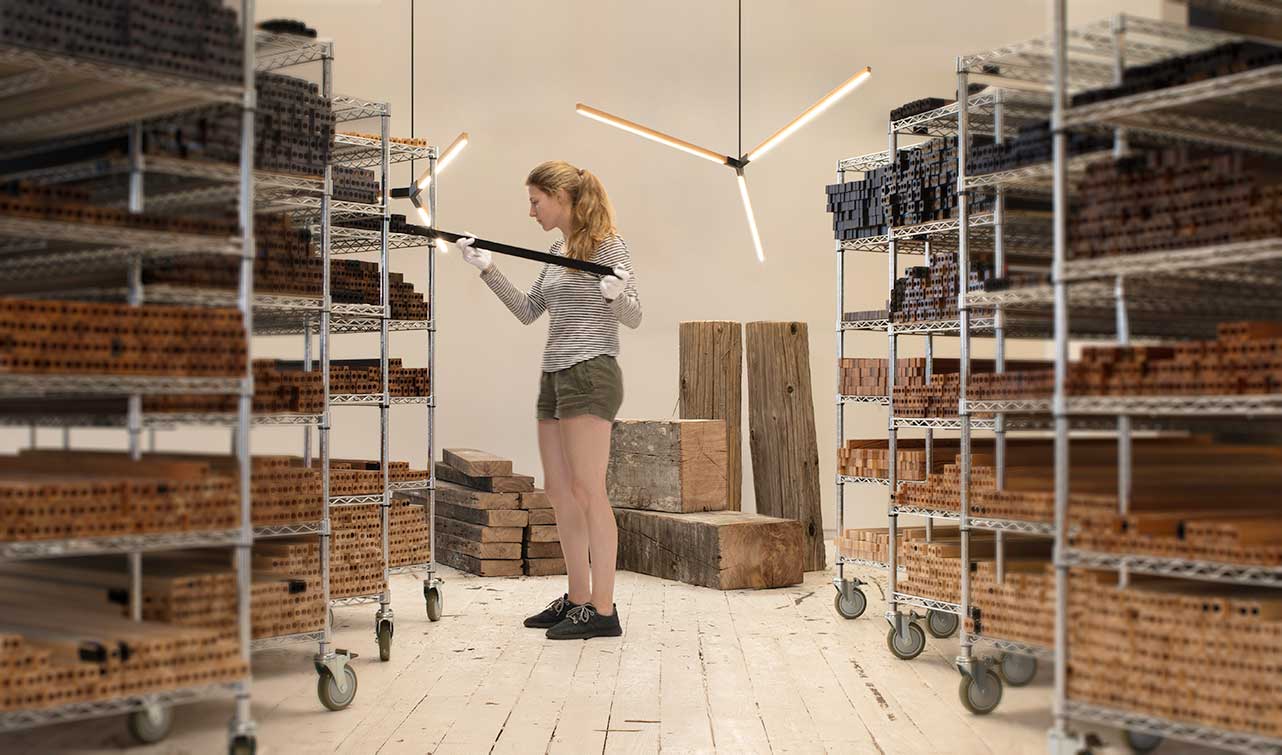
Long Island City-based Stickbulb uses reclaimed timber—sourced from New York’s decommissioned water towers, among other sites—to make sleek light fixtures is
An example of this in action is Stickbulb’s X connector—a cast brass piece with concave detail that beautifully reflects light and holds four sticks together. In creating it, a world of possibilities was unlocked. “It creates a whole world of geometry—our Truss collection, Boom collection, a small side table called the X Table, our Triple X Chandelier,” Chris says. “When we first conceived of the X connector, it was for one set of fixtures. We realized it had this potential to make all these other geometries because we literally create little toy versions of all of our fixtures. We have tiny little connectors we can throw out on a table. We have tiny little measure sticks, and we play with them like Erector Sets and see what we can come up with.”
“I spend a tremendous part of time protecting my brain from the radiation of everything else that’s going on.”
A dozen full-time employees and some interns collaborate in the open space that is Stickbulb’s studio in Queens. “Everything flows from one department to the next—even flowing between our design space, production, and showroom space,” Chris says. There’s a kind of constant feedback loop, with frequent conversations, design tweaks, and other improvements made quickly. “We like the nimbleness that offers us and the ability to be constantly doing better, sometimes in very invisible ways.”
- A common stick links two fixtures into one in the Double Boom design.
- A closer look at the X connector, a versatile and light-reflective joint component that fastens together light sticks in several of Stickbulb’s fixtures.
Russell says the team has enough inspiration that they don’t get too caught up in what others do. “Part of my job as creative director is to make sure we have a vision of what we are doing. I spend a tremendous part of time protecting my brain from the radiation of everything else that’s going on,” he says. “We have a really beautiful closed loop system where we have great inspiration within our team, we have great people to act on and realize that inspiration, and we have the craftspeople to make those things and the marketing and sales team to help sell those things. If you have a good team, it just starts to hum on its own.”
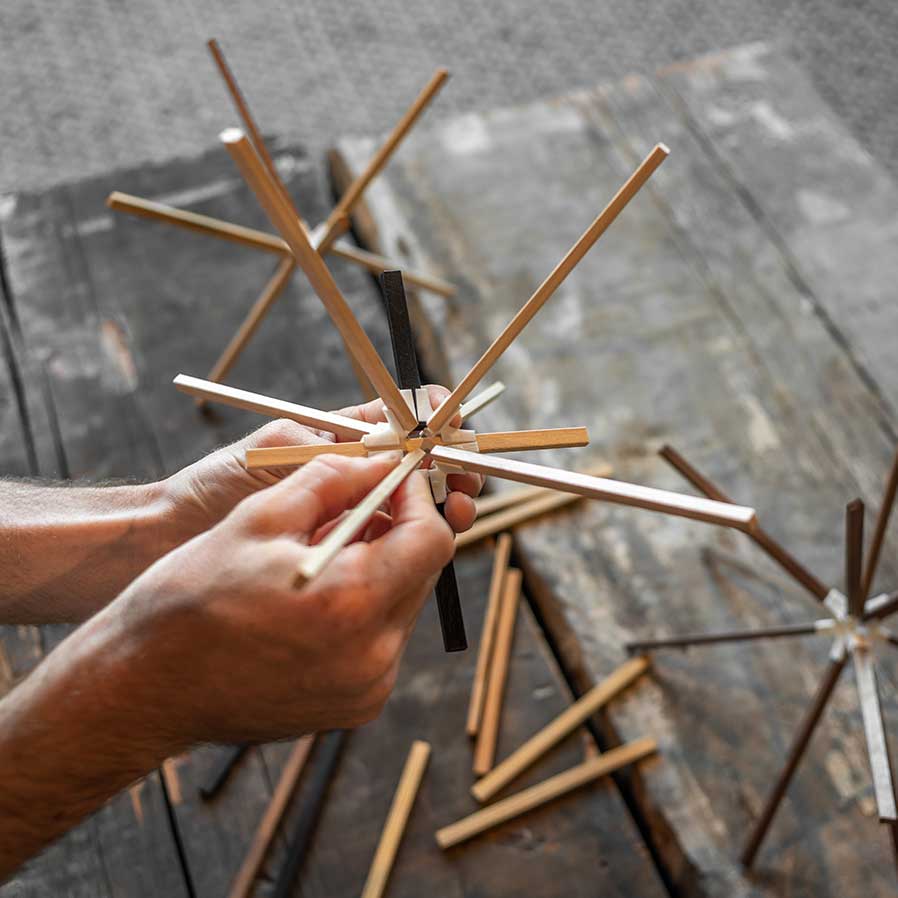
‘We have not deviated from the same stick profile. It comes in different lengths, and over the years we folded in a few new wood species as options,’ Chris says. Pictured here is an example of the ‘little toy versions’ that Stickbulb creates as part of the design process.
Stickbulb has always emphasized sustainability, too. “If we’re going to be building things, using resources, and putting things out into the world, we feel a sense of responsibility to do that in the best way we can—both from a quality perspective but also in the responsible use of materials perspective,” Chris says.
Chris and Russell loved the idea of giving new life to materials. Their woods are repurposed and tell a story—just look at the Fire and Ice collection, which incorporates ruins from the Chicago Pullman Couch factory. It’s interesting work considering their background. “Rather than designing new buildings we’re brushing up against old and decaying ones,” Russell says. “It’s an interesting shift in perspective from being in school, trying to come up with these new structures and spatial concepts, never thinking we’d be feeding off of 100-year-old buildings that have outlived their use or been demolished or burned down.”
- Stickbulb’s recent Fire and Ice installation at the Luminaire Chicago showroom featured fixtures made from wood salvaged from the Pullman Couch factory building…
- …The old building was destroyed by fire in sub-zero temperatures in Chicago, encasing its exterior in ice from the fire hoses while the building’s interior burned.
Stickbulb also uses redwood from New York City water towers reaching the end of their useful lives, having been installed roughly 40 years ago, back when people were harvesting old growth redwood trees. “We have access to a quality wood material you flat-out just can’t get this day and age,” Chris says.
This article originally appeared in the Spring/Summer 2019 issue of Sixtysix with the headline “RUX Studios on Stickbulb.” Subscribe today.
PRODUCTION CREDITS:
Produced by Studio Sixtysix
Words by Laura Rote
Photos courtesy of Stickbulb
Studio Sixtysix is the in-house creative agency to Sixtysix magazine. Studio Sixtysix stories are conceived, produced, and edited by Studio Sixtysix.