Inside The Waterlands in St. Petersburg, Florida, Bill Hamilton and his crew of seven toil away on an unlikely product—vintage style clawfoot tubs. Sparks fly, the polisher whizzes and groans, and Bill himself tinkers at the computer, reinterpreting a 19th century design to make it fit modern lifestyles—with more room to soak and updated plumbing.
The Waterlands Bathtub Company is Bill’s latest project, one of many successful businesses he’s started, but don’t call him CEO. “I don’t like the way it sounds. It sounds so formal,” he laughs. Bill moved to Florida in 2002, but his Scottish heritage influences everything he does. He recalls fondly his time growing up on a farm, The Waterlands’ namesake, between Edinburgh and Glasgow. “The Waterlands was my grandfather’s farm in Scotland where I used to spend most of my time as a kid. A lot of inspiration comes from that time when you’d see old clawfoot tubs, some functional and some repurposed as troughs or gardens,” he says. “Farms are full of shapes and colors and metals—rusting metals and decaying metals. It was a fabulous place to grow up.”
Those color-changing metals are seen in the work Bill does today. “Our customers tell us our bathtubs are more like works of art than bathtubs. I consider this the ultimate compliment. This is our goal,” he says.
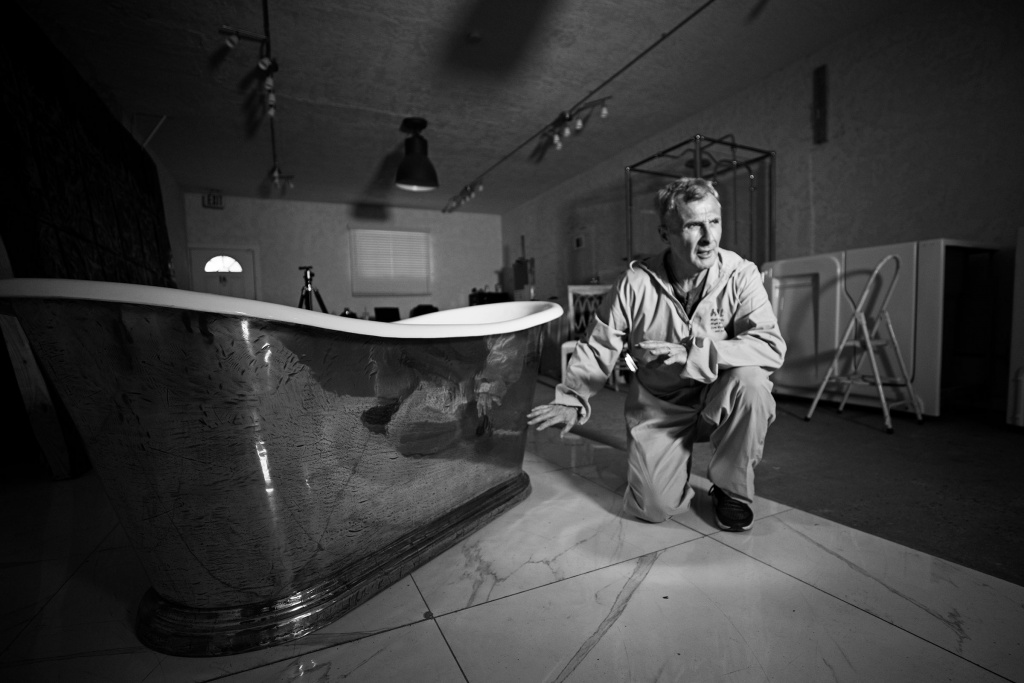
The Waterlands’ Founder Bill Hamilton dreams of vintage-style designs. Photo by Tony Smailagic
What inspired you to do this work?
It goes back to my childhood when I used to have a paper run. I delivered to a pig farm, and there was a foundry across the road. Sometimes on cold mornings I’d stick my nose in and see the fires and talk to the blacksmith. It was a small village—15,000 people. I’d see these things coming out of the mold and always loved the markings.
Later in life I’d go to antique shops in London. I saw this stunning Chariot bathtub that was made by Rogeat in Lyon in the 1850s. I thought it was beautiful, and I wondered if we could do something similar. I went to several manufacturers worldwide to try to find someone who could do this with us. It took almost a year, and we eventually found a willing partner just outside of Beijing. We walked through the issues—it wasn’t as easy as I’d hoped—but I managed to get the first tub after about four years of pestering people.
Where does the design begin?
Sometimes we’ll make shapes out of metal in the workshop; sometimes we’ll make a rendering on the computer. We’ll discuss what we’re looking for and get the concept and dimensions the way we want, and we’ll quite often manufacture a piece to send to the factory and say, “We need this piece cast.” So we’ll often make a part of a tub, send it to the factory, and let them produce our model in cast iron.
- Much of Bill Hamilton’s time is spent sketching. Photo by Tony Smailagic
- The Waterlands’ CEO does a lot of handwork on the vintage-style tubs himself. Photo by Tony Smailagic
What makes your finishes so special?
We try to leave “living” finishes as often as we can. The copper and brass will change. The customer can maintain the finish if they like, but we try to leave it so the finish will change over the years in its environment because we think that’s an exciting part of the tub’s life and for the person who buys it to see it change gradually.
- No Waterlands tub is like the other, as different marks and stress lines occur during the cooling process. Photo by Tony Smailagic
- Founder Bill Hamilton loves the way each tub changes over time. Photo by Tony Smailagic
What makes the new design special?
We learned people were going away from doing old cast iron versions of tubs and making metal shells, but they don’t show any character. When we found someone who’d make our tubs the way we wanted, the same as they’d been made in 1850, that was exciting. With that manufacturer we make the small range we offer now—about five tubs with different sizes and finishes.
Now the tubs come to our workshop and we do all the necessary finishing. They’re in a raw state when they come to us. I don’t think anyone will ever produce anything like these. There’s such a learning curve and you have to have such an understanding of engineering concepts to do the metal exterior, I just really don’t see anyone else jumping into the business.
What does your day-to-day process look like?
There are seven people in the workshop, excluding myself. I come up with a new finish and decide what we’ll do. We’ll develop that and perform the coating process. There will be maybe four people working on one bathtub before it gets to the final stages, and there’s not a tub that goes out without me looking at it. Every tub is very personalized. It probably takes three weeks from starting a tub to finishing. We have to shot blast it, sand it down, do an initial stain, and then wait between coatings. Your final prep work can sometimes take five days just to finish one tub.

On any given day you’ll find a small crew working on custom tubs at The Waterlands. Photo by Tony Smailagic
How do your engineering and business backgrounds influence this work?
I used to do metal work, pipeline engineering. I started my first business in 1980—an engineering business. A lot of people think starting businesses is difficult, but I love it. The idea of starting The Waterlands was easy. When you look at all the things you’ve done before, it all lends to your current business. I didn’t want to just buy and sell things. I wanted to make products. I suppose that comes from the farm. You were always working on the farm, but it never felt like work because it was so much fun. This business is like that.
LEARN MORE: HERE
This article originally appeared in the Spring/Summer 2020 issue of Sixtysix with the headline “Bill Hamilton: Designer.” Subscribe today.
PRODUCTION CREDITS
Produced by Studio Sixtysix
Words by Laura Rote
Photos by Toni Smailagic
Studio Sixtysix is the in-house creative agency to Sixtysix magazine. Studio Sixtysix stories are conceived, produced, and edited by Studio Sixtysix.