The sleek, 3-inch Impinda is the genius of Oregon knife-maker Bill Harsey. “I simply wanted a good, small knife to go fishing with—something useful for fly-fishing for trout. I’d always thought, ‘Wouldn’t it be great if you had a knife that was useful in the outdoors that you could have in your pocket all day long, no matter what you’re doing?’” Long known as a tactical knife maker—he’s been making knives for military special forces since the ’80s—Bill wanted to make something simpler.
The Impinda is built for safety, emphasizing the relationship between blade and spring as a slip joint and non-locking knife. It manages pressure at every point of contact using a differential spring pressure. The balance creates a smoother opening, safer closing, and positive engagement in the fully open position. “A traditional slip joint knife has been an American tradition forever. This is a traditional slip joint that has enough strength to open safely that also closes safely,” Bill says.
“Some of the trends I see in the knife world are unbelievable. Everybody is fighting for a powerful graphic image to display on a computer. This has caused a serious form of what I call internet inbreeding. It drives me a bit crazy,” he says, adding that everybody copies everybody. But that isn’t so with the Impinda. In fact, you won’t find anything quite like it.
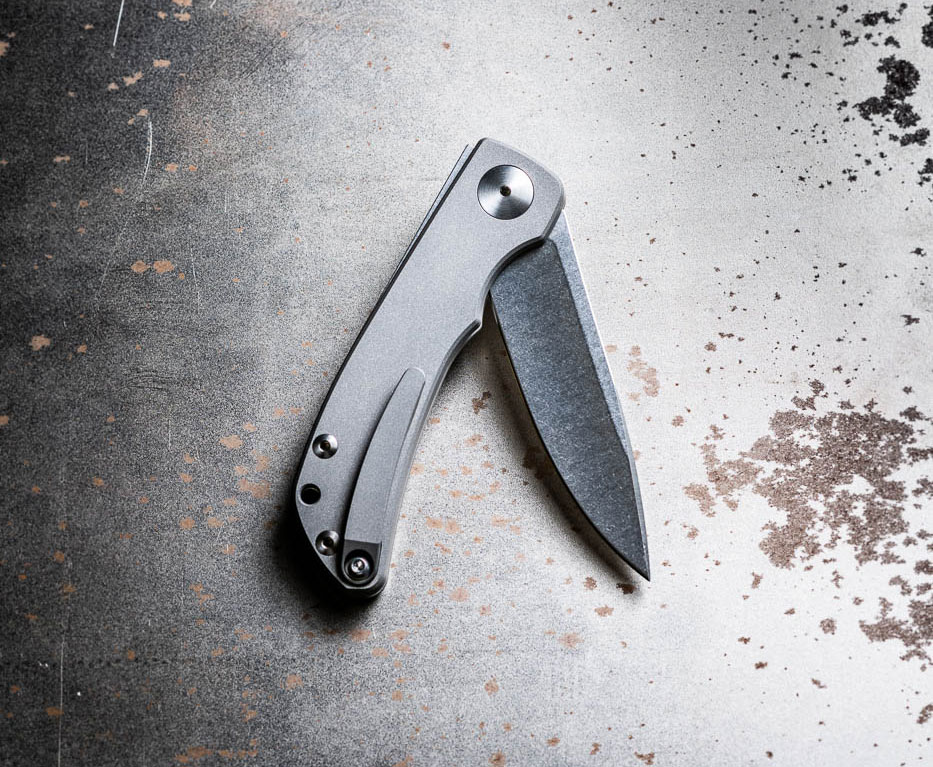
Photo by Chris Force, prop styling by Kristina Walton Zapata
How It’s Made
Bill doesn’t design any of his knives using CAD/CAM. “I’m a believer in pencil and paper to Lexan to hand-modeling. I’m making a knife that’s going to be used and felt by the human hand, so I’m going to have my hand in every step of the way.” He says the knife wouldn’t be possible without CRK’s formidable ability to produce very high tolerance knives.
How It Evolved
The knife evolved from the lessons of designing and manufacturing tactical knives to make a modern pocketknife. The Chris Reeve Knives team had seen a resurgence in slip joint knives in the last several years, but they’d never seen a spring mechanism as innovative as this.
The Materials
In 2009, Bill and Chris Reeve worked with the team of metallurgists at Crucible Industries to test and develop the blade steel—CPM S35VN. “This steel has never been used as a spring before,” he says. “That’s an exotic steel. We have a much higher toughness, ductility, and holdability.” Bill and Tim Reeve worked with the same metallurgists to ascertain that a spring was indeed a suitable application for S35VN.
The Specs
The scale of the knife and blade shape was crucial. Bill wanted a working field blade with enough point to be useful if needed. “The scale of the knife was determined on pocketability.”
Break It Down
Bill says traditional jackknives are hard-riveted together or pinned so you can’t take them apart if you want to clean them. “What we’re making you can completely disassemble because we’re using all heat-treated screws. All the screws can be unbolted with a simple hex key.”
Buy it: The Impinda, $450
This article originally appeared in the Fall/Winter 2018 issue of Sixtysix with the headline “The Impinda.” Subscribe today.
PRODUCTION CREDITS
Produced by Studio Sixtysix
Words by Laura Rote
Photos by Chris Force
Styling by Kristina Walton Zapata
Studio Sixtysix is the in-house creative agency to Sixtysix magazine. Studio Sixtysix stories are conceived, produced, and edited by Studio Sixtysix.